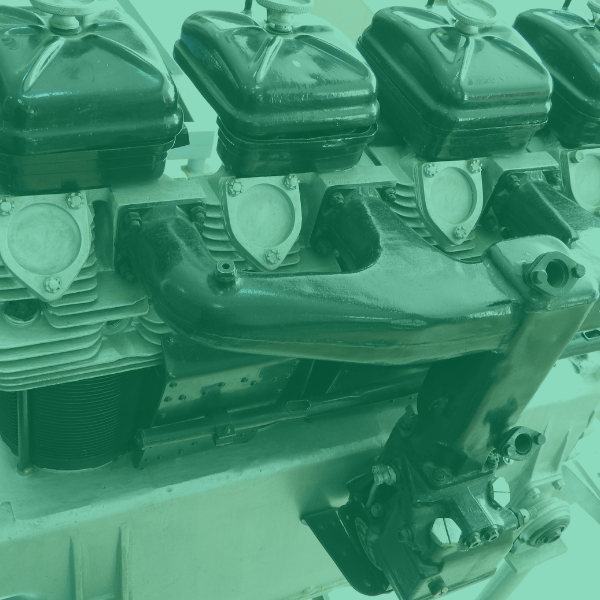
The Evolution and Materials of Combustion Chambers and Their Modern Maintenance
Share
The combustion chamber is a pivotal component of internal combustion engines, evolving significantly over time to improve performance, efficiency, and emissions control. Let's delve into its historical evolution, the materials used in its construction, and how modern additives like Berryman Intake Valve & Combustion Chamber Cleaner are vital in maintaining its optimal function.
Historical Evolution of Combustion Chambers
Combustion chambers have undergone substantial transformations since their inception. Early designs in the late 19th and early 20th centuries were rudimentary, primarily focusing on containing the explosion of the air-fuel mixture. These initial chambers were crafted from heavy cast iron, prioritizing durability over performance.
As automotive technology advanced, so did the design of combustion chambers. The introduction of aluminum alloys in the mid-20th century marked a significant shift. Aluminum’s lightweight properties and superior thermal conductivity compared to iron allowed for better heat management, contributing to more efficient engine operation and reduced weight. This shift played a crucial role in enhancing fuel economy and engine performance.
In the modern era, the focus has shifted towards maximizing efficiency and reducing emissions. Advanced designs like hemispherical ("hemi") chambers, pent-roof chambers, and bowl-in-piston configurations emerged, each optimizing the swirl and turbulence of the air-fuel mixture for more complete combustion. Additionally, modern engines often employ direct fuel injection (GDI) systems, which necessitate even more precise combustion chamber designs to handle higher pressures and more aggressive fuel delivery.
Materials Used in Combustion Chambers
Materials science has continually evolved to meet the increasing demands on combustion chambers. Here’s a look at the common materials used:
-
Cast Iron:
- Early Use: Initially used for its durability and ease of manufacturing.
- Advantages: High strength and wear resistance.
- Disadvantages: Heavy and poor thermal conductivity, leading to higher engine weight and inefficient heat dissipation.
-
Aluminum Alloys:
- Mid-20th Century Onward: Became the standard due to their lightweight and excellent thermal conductivity.
- Advantages: Lighter than cast iron, better heat management, leading to increased performance and fuel efficiency.
- Disadvantages: Lower strength at high temperatures compared to iron, requiring additional cooling and design considerations.
-
Ceramics and Advanced Composites:
- Recent Developments: Used in high-performance and racing engines.
- Advantages: Extremely high-temperature resistance, minimal thermal expansion, and superior wear resistance.
- Disadvantages: High cost and complexity in manufacturing.
The choice of material is influenced by factors such as the intended use of the engine, performance requirements, and cost constraints. Modern engines often employ a combination of these materials, optimizing each for different parts of the combustion chamber to balance performance and durability.
Modern Maintenance: The Role of Additives
Maintaining a clean and efficient combustion chamber is crucial for modern engines, especially those utilizing advanced technologies like GDI, PFI, and TBI systems. Over time, carbon deposits can accumulate within the combustion chamber and on intake valves, leading to reduced performance, increased emissions, and higher fuel consumption.
Berryman Intake Valve & Combustion Chamber Cleaner is a specialized solution designed to address these challenges. Formulated with polyetheramine (PEA), it effectively dissolves stubborn carbon buildup, restoring engine performance and drivability. PEA is particularly effective at breaking down carbon deposits, ensuring that combustion chambers and intake valves are kept clean.
By using Berryman's cleaner, engines can maintain their original octane requirements, leading to more efficient combustion and reducing the likelihood of knocking. Its compatibility with various fuel-injected gasoline engines and safety for catalytic converters and oxygen sensors make it a versatile and reliable choice for regular maintenance.
The evolution of combustion chambers and the materials used in their construction underscore the importance of ongoing maintenance to ensure optimal engine performance. Additives like Berryman Intake Valve & Combustion Chamber Cleaner provide a practical and effective solution for maintaining the cleanliness and efficiency of these critical engine components, enhancing the overall longevity and performance of modern engines.